En el campo de excavadorasLa elección entre motores de inyección directa e inyección electrónica puede afectar significativamente el rendimiento, la eficiencia de combustible, las emisiones y el mantenimiento. Comprender estas diferencias es fundamental para tomar decisiones informadas.
1. Sistema de inyección de combustible
Excavadoras de inyección directa:En un sistema de inyección directa, el combustible se rocía directamente en la cámara de combustión de cada cilindro. Las bombas de combustible de alta presión impulsan el combustible a través de boquillas de precisión a presiones que normalmente oscilan entre 100 y 200 bares o incluso más. Por ejemplo, algunos modelos avanzados pueden alcanzar hasta 300 bares. Esto permite un control extremadamente preciso de la cantidad de combustible y el momento de la inyección, lo que garantiza una combustión óptima. La boquilla de combustible está ubicada estratégicamente dentro de la culata para lograr la mejor mezcla de combustible y aire.
Excavadoras de inyección electrónica:Los sistemas de inyección electrónica, por otro lado, inyectan combustible en el colector de admisión. El combustible se mezcla con el aire entrante en el colector antes de ingresar a la cámara de combustión. La presión de inyección es relativamente más baja, generalmente alrededor de 3 a 5 bares. La unidad de control electrónico (ECU) monitorea varios parámetros del motor y ajusta la cantidad y el momento de inyección de combustible en consecuencia. Este sistema es más sencillo en comparación con la inyección directa, pero ofrece un control menos preciso dentro de la cámara de combustión.
2. Eficiencia de combustible
Inyección directa:Las excavadoras de inyección directa generalmente muestran una mejor eficiencia de combustible. Al inyectar combustible directamente en la cámara de combustión, pueden lograr un proceso de combustión más completo. En ciertas condiciones de operación, como durante trabajos de carga ligera a media, pueden realizar operaciones de combustión pobre. La combustión pobre significa operar con una relación aire-combustible mayor que la relación estequiométrica (alrededor de 14,7:1), lo que reduce el consumo de combustible. Los estudios han demostrado que, en comparación con los motores de inyección electrónica, la inyección directa puede generar ahorros de combustible de hasta 10% - 15% en algunos casos.
Inyección electrónica:Los motores de inyección electrónica son relativamente menos eficientes en cuanto al consumo de combustible. Dado que el combustible se mezcla previamente en el colector de admisión, una parte del mismo puede adherirse a las paredes del colector y no participar completamente en la combustión. Esto genera cierto desperdicio de combustible. Además, no pueden ejecutar las precisas estrategias de combustión pobre que pueden ejecutar los motores de inyección directa, lo que da como resultado un mayor consumo de combustible con cargas de trabajo similares.
3. Rendimiento energético
Inyección directa:Estas excavadoras ofrecen un rendimiento de potencia superior. Cuando se necesita alta potencia, por ejemplo, durante operaciones de excavación rápida o de elevación pesada, el sistema de inyección directa puede inyectar rápidamente una gran cantidad de combustible en la cámara de combustión. Esta inyección rápida permite la formación de una rica mezcla de combustible y aire que se quema de forma explosiva, generando una potencia significativa. Muchas excavadoras de inyección directa modernas pueden alcanzar un par máximo a velocidades del motor relativamente bajas, normalmente entre 1500 y 2000 revoluciones por minuto, lo que proporciona una excelente aceleración y capacidad de trabajo.
Inyección electrónica:Las excavadoras de inyección electrónica tienen una potencia de salida más lineal y estable. La mezcla de combustible y aire que se forma en el colector de admisión antes de entrar en la cámara de combustión produce un proceso de combustión más gradual. Esto da como resultado una entrega de potencia más uniforme sin las ráfagas repentinas de potencia características de la inyección directa. Si bien esto puede ser ventajoso en aplicaciones en las que se desea una entrega de potencia uniforme y constante, como en algunas tareas de nivelación de precisión, en términos de potencia de salida pura, generalmente quedan por detrás de los motores de inyección directa de la misma cilindrada.
4. Rendimiento de emisiones
Inyección directa:Las excavadoras de inyección directa tienen ventajas y desafíos en términos de emisiones. El lado positivo es que pueden reducir eficazmente las emisiones de monóxido de carbono (CO) e hidrocarburos (HC) mediante un control preciso de la combustión. Por ejemplo, los motores de inyección directa avanzados con técnicas de combustión estratificada pueden minimizar las emisiones contaminantes durante las fases de arranque y ralentí del motor. Sin embargo, debido al entorno de alta temperatura y alta presión en la cámara de combustión, tienden a producir más óxidos de nitrógeno (NOx). Para cumplir con los estrictos estándares de emisiones, a menudo se requieren sistemas de postratamiento complejos como la reducción catalítica selectiva (SCR) o la recirculación de gases de escape (EGR).
Inyección electrónica:Las excavadoras con inyección electrónica tienen un rendimiento de emisiones relativamente estable. El proceso de combustión más uniforme debido a la premezcla de combustible y aire en el colector de admisión da como resultado menos emisiones de NOx en algunas condiciones de funcionamiento. Sin embargo, durante los arranques en frío, la formación de una mezcla de combustible y aire menos que ideal puede provocar un aumento de las emisiones de HC. En general, si bien no exigen sistemas de control de emisiones tan complejos como los motores de inyección directa, sigue siendo necesaria una optimización continua para cumplir con las cambiantes regulaciones sobre emisiones.
5. Costo de mantenimiento y confiabilidad
Inyección directa:Los costos de mantenimiento de las excavadoras de inyección directa suelen ser más altos. El sistema de combustible de alta presión requiere combustible de alta calidad. El uso de combustible de mala calidad puede obstruir las boquillas de combustible, que están expuestas directamente al duro entorno de la cámara de combustión y son propensas a la acumulación de carbón. Los depósitos de carbón en las boquillas pueden afectar la precisión de la inyección de combustible y el rendimiento del motor. Además, los complejos sistemas de postratamiento aumentan la complejidad y el costo del mantenimiento. Sin embargo, con los avances tecnológicos continuos, su confiabilidad está mejorando.
Inyección electrónica:Las excavadoras de inyección electrónica tienen menores costos de mantenimiento. La menor presión de inyección significa que las boquillas de combustible tienen menos probabilidades de sufrir daños por alta presión. Su estructura relativamente simple, sin los intrincados sistemas de control de combustión y postratamiento de los motores de inyección directa, las hace menos propensas a fallas durante el uso a largo plazo. En términos de reparación, el reemplazo de piezas y las técnicas de reparación son más maduras, lo que les da una ventaja en términos de costo de mantenimiento y confiabilidad.
En conclusión, al elegir entre una excavadora de inyección directa y una de inyección electrónica, es esencial tener en cuenta los requisitos específicos del trabajo, como la carga de trabajo, las necesidades de ahorro de combustible, las normas sobre emisiones y las capacidades de mantenimiento. Cada tipo tiene su propio conjunto de fortalezas y debilidades, y la elección óptima variará según el entorno operativo y los escenarios de uso.SY365 es el modelo más vendido entre las excavadoras de inyección directa. Los modelos de inyección electrónica más vendidos incluyen pc200-8, gato320d2,ZX200,etc.
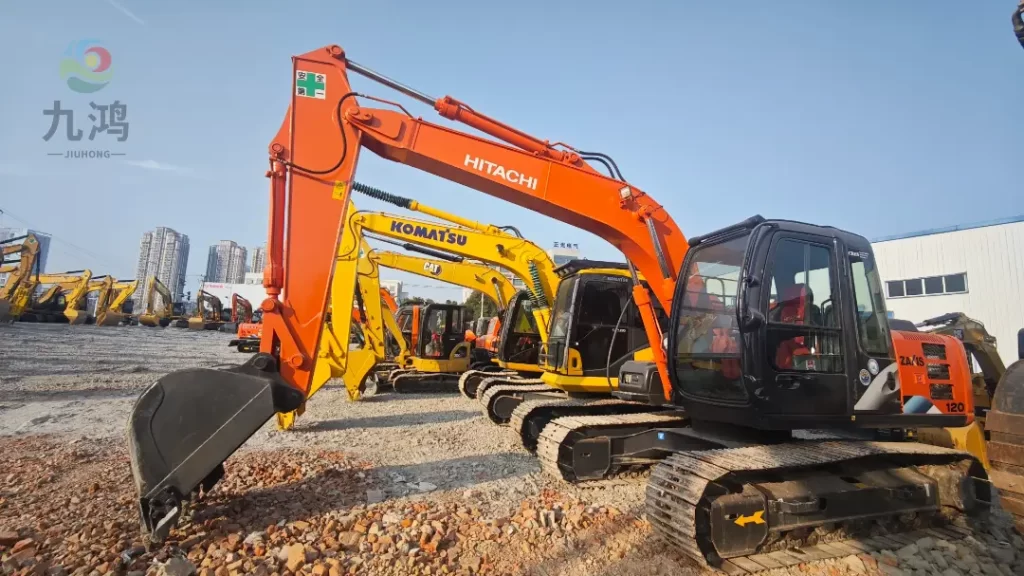
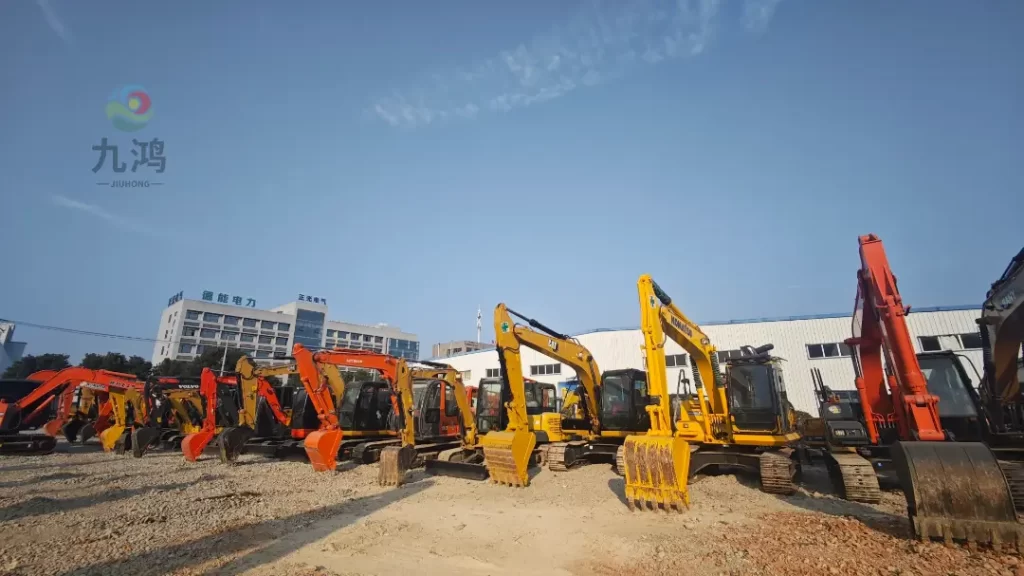